Mastering Gauge Fillet Welds: Tips for Perfect Measurements and Implementation
Mastering Gauge Fillet Welds: Tips for Perfect Measurements and Implementation
Blog Article
The Ultimate Guide to Fillet Weld Quality Assurance: Ensuring Strength and Longevity in Your Welded Joints
In the world of welding, making sure the strength and sturdiness of fillet welds is critical for the integrity of bonded joints. The quality control measures executed during the welding process can significantly influence the structural sturdiness of the final product. From the choice of appropriate materials to the careful examination of welds, each action plays a vital function in identifying the general high quality of the weld joint. As we start this exploration of fillet weld quality assurance, we will reveal important elements that affect weld strength, dive into effective examination approaches, and review approaches for preventing usual weld issues. Stay tuned to uncover just how understanding these methods can raise the durability and integrity of your bonded joints.
Importance of Fillet Weld Quality Assurance
Ensuring correct fillet weld top quality control is extremely important in ensuring the structural honesty and longevity of welded components in different industries. Fillet welds are generally made use of in structural steelwork, bridges, stress vessels, pipelines, and various other essential facilities where the strength of the weld is vital to general safety and performance. Quality control procedures such as visual inspections, non-destructive testing, and adherence to welding treatments assist recognize potential defects like lack of combination, incomplete infiltration, damaging, or extreme reinforcement.
Trick Variables Impacting Weld Strength
Achieving optimum weld toughness calls for careful consideration of various essential variables that influence the integrity and resilience of the bonded joint. The first essential factor is proper joint prep work, which involves cleaning up the base steels to get rid of any type of impurities that could weaken the weld. Furthermore, the fit-up of the joint is necessary to ensure correct penetration and blend of the filler material.
The choice of the suitable welding method and specifications likewise plays a considerable duty in establishing weld strength. Aspects such as warm input, travel rate, and electrode angle can affect the top quality of the weld. Maintaining the correct interpass temperature throughout multi-pass welding is crucial to protect against fracturing and make sure a solid bond in between the layers.
Moreover, the option of filler product and its compatibility with the base metals is important for attaining high weld toughness. Utilizing filler material with the proper mechanical residential properties can enhance the general integrity of the weld. Lastly, post-weld warm therapy and proper assessment techniques are essential actions in making sure the strength and toughness of the welded joint.
Inspection Approaches for Weld Integrity
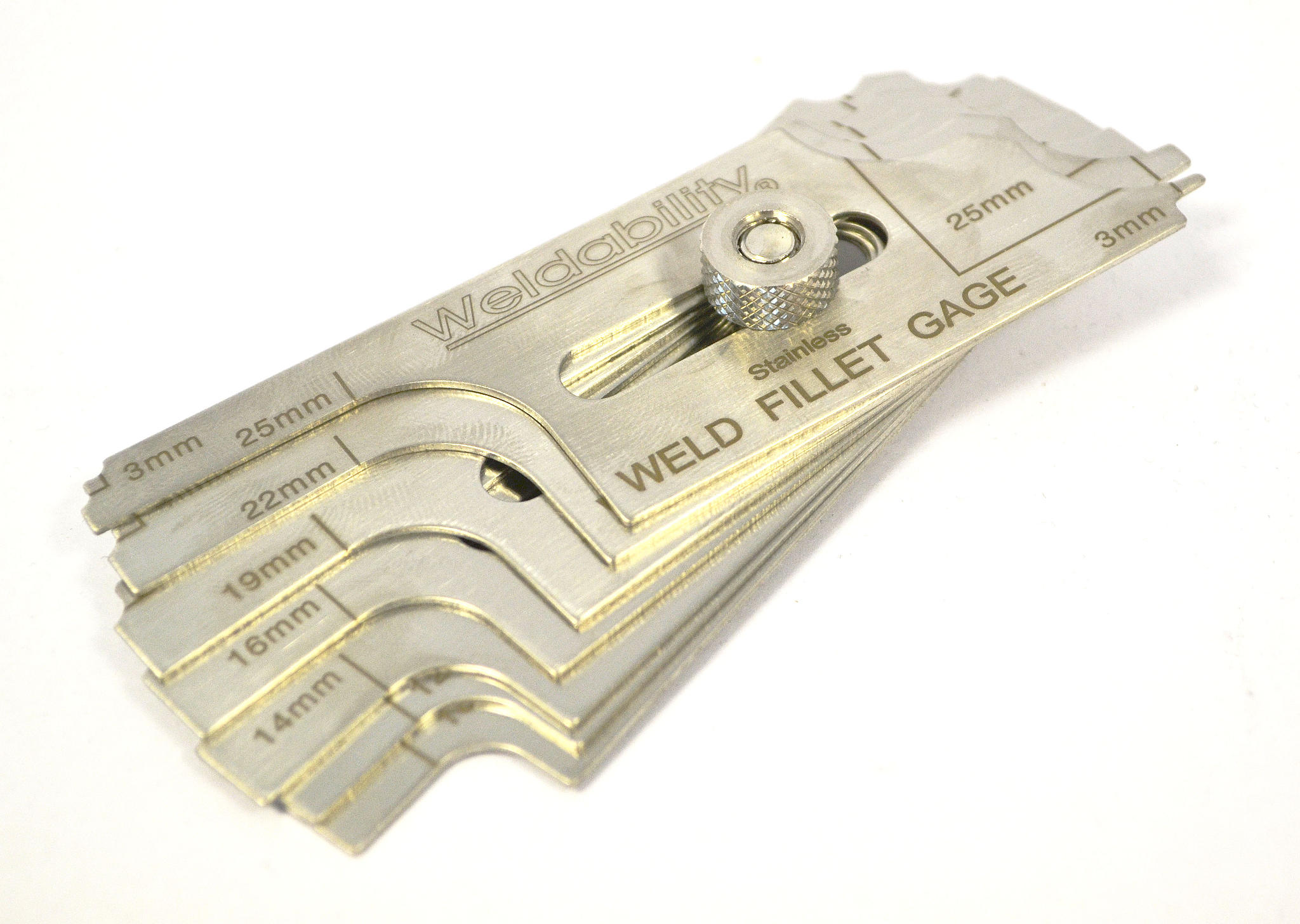
An additional crucial evaluation technique is liquid penetrant testing, where a liquid dye is related to the weld surface area - Gauge Fillet Weld. The dye seeps into any type of surface-breaking flaws, making them noticeable under UV light. This technique is efficient for identifying flaws that might not be noticeable to the nude eye
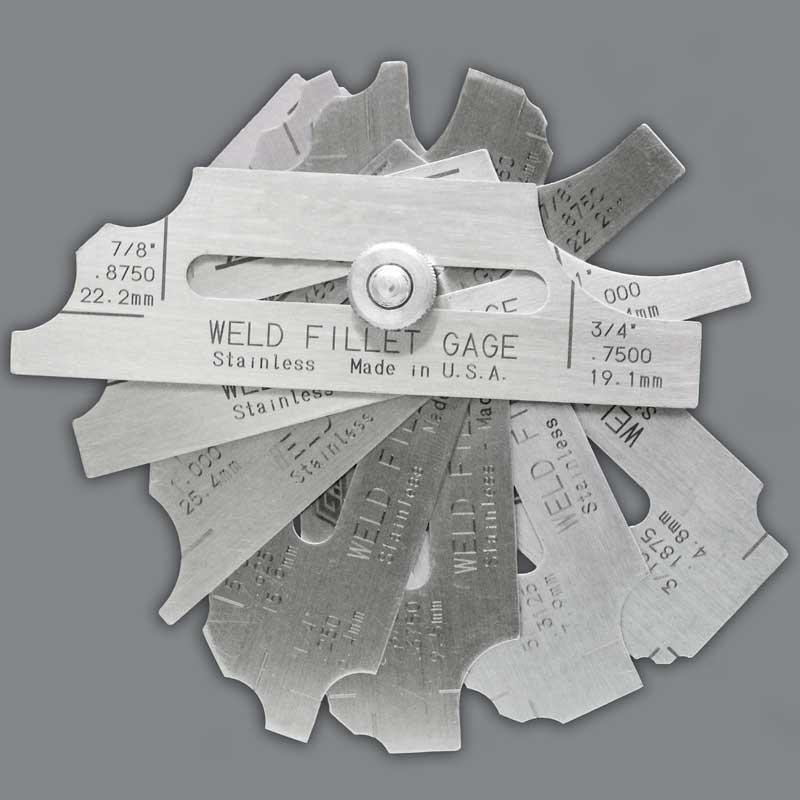

Ultrasonic screening is also commonly used for checking weld integrity. High-frequency acoustic wave are directed into the weld, and any kind of interruptions in the audio wave pattern indicate possible defects like fractures or absence of fusion.
These assessment methods play a crucial duty in guaranteeing the top quality and reliability of welds, eventually adding to the overall strength and toughness of bonded joints in industrial settings.
Stopping Typical Weld Flaws
In order to keep the architectural integrity of welded joints in commercial applications, it is important to carry out safety nets to attend to usual weld defects. One typical problem is absence of combination, where the filler material stops working to bond sufficiently with the base metals, leading to weak try this web-site spots in the weld. This can be prevented by making sure correct warmth control and using the correct welding strategy.
Another regular issue is porosity, caused by gas entrapment in the weld metal during the welding procedure. To avoid this, it is crucial to clean up the base steels thoroughly, use completely dry electrodes, and keep an appropriate welding setting with appropriate ventilation.
Furthermore, fractures in welds can jeopardize the joint's toughness. To prevent this issue, it is necessary to regulate the cooling rate after welding, use pre-heating when essential, and select appropriate welding criteria.
Enhancing Bonded Longevity With Correct Strategies
To strengthen the durability and dependability of welded structures, employing innovative welding strategies is crucial. One essential technique to boost weld sturdiness is to make certain proper weld bead placement. By positioning the weld grain properly within the joint, the weld's stamina and resistance to exhaustion can be considerably imp source enhanced. In addition, utilizing the appropriate welding criteria, such as voltage, current, and take a trip rate, is crucial for achieving a resilient weld. These specifications directly influence the weld's infiltration, blend, and general high quality, adding to its durability.
Picking the ideal filler metal and ensuring the cleanliness of the base steels can prevent incorporations and various other issues that could jeopardize the weld's durability. By carrying out these proper methods, welders can guarantee that their welded joints exhibit exceptional stamina and resilience, fulfilling the highest possible top quality standards.
Final Thought
To conclude, preserving top quality control requirements for fillet welds is crucial for making certain the toughness and longevity of welded joints. By comprehending the vital factors affecting weld stamina, utilizing assessment techniques for weld integrity, preventing common weld problems, and employing correct strategies, welders can improve the overall longevity of their welds. It is essential to prioritize top quality control procedures to produce reliable and resilient bonded joints.
In the realm of welding, making sure the strength and toughness of fillet welds is critical for the stability of welded joints. As we begin on this exploration of fillet weld top quality control, we will certainly uncover essential aspects that affect weld strength, dig into effective inspection methods, and go over techniques for preventing typical weld issues.Attaining optimal weld strength requires cautious factor to consider of various key elements that influence the integrity and durability of the welded joint (Gauge Fillet Weld).In final thought, maintaining high quality control requirements for fillet welds is essential for guaranteeing the strength and longevity of bonded joints. By recognizing the essential aspects influencing weld strength, using evaluation methods for weld stability, protecting against common weld flaws, and utilizing correct strategies, welders can boost the overall sturdiness of their welds
Report this page